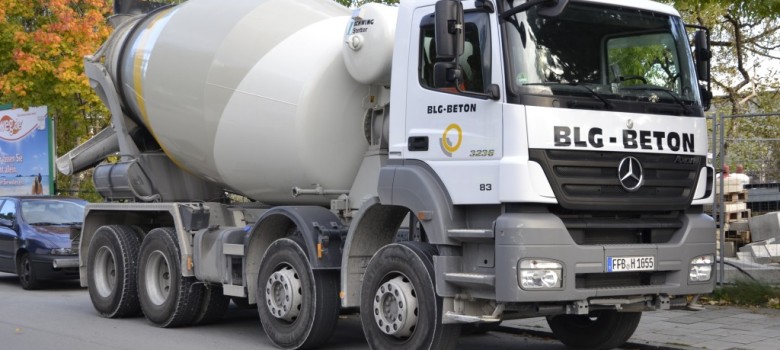
First off, I would like to apologise – this subject really is very dry! I have tried to make the blog below as interesting as possible, but it was a bit of a struggle… You might want to grab a strong coffee before you get started!
So here goes…..
Concrete is the most widely used building material today as a result of its strength and its durability. It is used in homes, airports, skyscrapers, tunnels and pretty much every other type of construction you can think of.
Concrete and cement are terms that are often used interchangeably; however cement is actually an ingredient that makes up concrete, along with water, sand and gravel. Cement acts as a hydraulic binding material, hardening with water and tying together all the aggregate materials.
Why is Concrete a Problem?
After coal-powered electricity, cement manufacture is the next biggest emitter of greenhouse gases, accounting for approximately 5% of annual anthropogenic global CO2 production. In 2011, we used approximately 3.6 million tonnes of the stuff within the construction industry – the problem being that for every tonne of cement produced, one tonne of CO2 is also produced.
I am not going to try to use this blog as a platform to preach that we should stop building – that would be ridiculous. People need a place to live and businesses need to grow. Instead, I am going to look at the current manufacturing processes and identify a few technologies and areas of investigation that are being toyed with; can these reduce the impact of the cement/concrete industry and the impact it has on anthropogenic CO2 emissions?
How is Cement Made?
First, a bit of science! To make cement, limestone (calcium carbonate – CaCO3) is heated to temperatures approaching 10000C, along with other feedstock materials such as clay (which contains silicates). At this temperature, the limestone (and other feedstock) breaks down into Calcium Oxide (known as Lime – CaO), Silicon Oxides and Carbon dioxide. The two oxides then combine to produce di & tri-calcium Silicate, which is then ground to a fine powder producing a product known as ‘clinker’.
Finally, gypsum is added to the clinker (to prevent flash setting of the cement), and this is ground to produce the cement, which can then be used as the main ingredient to make concrete.
There are two ways that making cement releases CO2:
- Burning fossil fuels to heat the kilns to achieve the reaction temperatures
- Breaking down calcium carbonate into calcium oxide and CO2
The burning of the fossil fuels accounts for about 30% of the total CO2, while breaking down the calcium carbonate accounts for 70%.
Processes to Make Cement Manufacture ‘Greener’
So how can you make ‘greener’ cement, thereby helping to reduce the total volume of carbon dioxide into the atmosphere?
Carbon Sequestration
Well strictly, the first couple of processes I touch upon are not related to changing the manufacturing process, but instead installing carbon sequestration techniques, thereby using the CO2-rich flue gasses to produce new materials.
As covered across TheGreenAge, there are numerous techniques of using carbon dioxide to produce useful products. Artificial photosynthesis would use this gas to produce sugars that are essentially a store of energy, replicating the natural process that plants use for growth everyday. The benefit of this technique would be not only limiting CO2 emissions, but also producing a valuable by-product.
Bio-algal synthesis is another technique for using the CO2; in this process the gas is pumped through a waste water growth medium infused with microalgae. These algae use sunlight and the CO2 for growth, doubling their mass every 24 hours, which can eventually be crushed for algae oil and algae meal for cattle. The advantage of the algae meal is that there is little cellulose within it (unlike regular crop-derived meal), so when digested by cattle, very little methane is produced (another greenhouse gas), helping to solve another greenhouse gas emitting problem.
In terms of changes to the process itself, there are numerous different ways that it could be carried out to produce lower carbon dioxide emissions.
Using Electrolysis to produce concrete
If electrolysis is used to react the limestone, replacing the initial kiln part of the reaction, different resulting molecules would be produced.
If carried out over 8000C, electrolysis would produce lime in addition to carbon and an oxygen molecule. If it is carried out under 8000C, the Lime is produced along with carbon monoxide and an oxygen atom. Carbon monoxide can be used to produce fuel and form plastics, and has a value of approximately $600 / tonne, allowing one to actually make money from the process (based on the lower cost to produce the lime).
Make Extra Strong Concrete, so you Need to Use Less!
This is a fairly simple idea, but by changing the feedstock entering the initial furnace, you can change the chemical composition of the clinker. So why not make ‘extra strong’ concrete, so you don’t need to use as much to perform the same job? Placticisers are additives that are added to the concrete that increase its strength. They are relatively complex but essentially to get strong concrete you need a low amount of water within it when it dries. These placticisers act as spacers between the cement molecules, ensuring that there is less water in contact with these molecules; hence stronger concrete.
Use Solar Power
The kilns used in the current process (to heat the clay and limestone) need to reach incredibly high temperatures. Historically, these temperatures have been reached by using the heat from burning fossil fuels (accounting for 30% of the carbon dioxide emissions from the cement manufacturing process). If the kilns were instead heated using a green electricity source, for example a concentrated solar power plant, this would obviously instantly remove much of the CO2 produced in the process.
Use Consistent mixes to make the concrete
Currently under EU standards there are 170 different types of concrete mix used in the construction industry. This poses a problem for builders, who simply do not know the strength of the different types, so in order to ‘make sure’ the construction is strong enough, excess concrete is used. If there were only say 10 types of concrete, then builders could better get to know the characteristics of each one, and they would be able to predict accurately how much of that particular type to use, thereby using less in the overall construction process.
The Future of Concrete
China currently use about half of the world’s supply of cement, and this demand is expected to rise. If current production techniques are used, an equivalent 700,000 tonnes of CO2 will enter the atmosphere.
This is just China though; hopefully in the next couple of years the worlds economies will be able to put the current financial situation behind them, and begin a new phase of growth. As a result, global demand for concrete is only going to rise, therefore we really need to come up with a way to lessen the impact of the concrete industry on the environment, potentially using one of the methods detailed above.
this article was excellent with the information that is within the article. i was just wondering, take old bathroom fixtures as additives to produce concrete? this would help with the carbon issue and would help to decrease waste in the landfills.
No it’s not. For starters coal fired plants are almost pollution free with the scrubbers we use.
I still thinks its bad for the environment.
No need for a strong coffee! It was an informative and brief article. I appreciate the emphasis on the need for concrete, yet directing responsibility to concrete producers to adopt environmentally friendly technologies to reduce carbon emissions. Thanks!
Thanks for explanation. We have a company – Brett Aggregates that want to put a concrete and aggregates plant near us in Sussex. I am concerned about the environmental impact – it is to be sited near a very lovely wild beach that we use regularly – and also the health implications on an area that already has poor air.
nice concrete evidence.
Thank you.
dab
whip ney ney
lols
Hey, great piece. is there any references?
Nice article. The number of concrete formulations are not all for structural purposes. These mixes were developed for specific applications such as marine applications, low strength fill, self expanding for filling of voids, non-shrink and the list goes on. As for the use of plasticizes this can add considerable cost, engineering of most concrete construction is based on cost verses performance.
I didn’t see any mention that the majority of concrete can be recycled into many other construction products at an economical price.
Yes concrete does have an energy input cost but compared to other building material it performs better and is a safer construction material, A concrete building or bridge does not fail in the same way as steel, concrete will show signs of warning long before failure.
Just remember that many early concrete structures last for hundreds of years. Humans just like having new things rather than old.
Unfortunately, we cannot throw solar power at all of our problems.
See this wired article: https://www.wired.com/story/a-solar-breakthrough-wont-solve-cements-carbon-problem/
In addition, using solar power to run the kilns only accounts for about 40 percent of cement’s carbon footprint.
I agree that concrete has large impact to the environment and we should consider alternatives and make acceptable compromises.
As the concrete sets I presume it re-absorbs carbon dioxide from the atmosphere to reform the hard carbonates. If this is the case, then the net amount of carbon dioxide released will be reduced to near-zero?
NO THE H2O EVAPORATES LEAVING THE BOUND ROCKS AND LIMESTONE
We need more carbon dioxide, if it gets cut that much more we’re going to start losing more and more plant life. Carbons plant food ya know…
Thanks for this informative article, this answers many of my questions regarding the carbon footprint of cement.
Seems like better steel reinforcements could reduce cement use too
i UNDERSTAND ABOUT THE 10 DEGREES TO MAKE KLINGET BUT HAVE YOU EVER WALKED BARE FOOT ON A CEMENT SIDEWALK THEN STEPPED OVER TO THE LAWN, THE LAWN IS NOT AS HOT. EVER WONDER WHY PIZZA OVENS ARE MADE OF CEWMENT BLOCKS it RETAINS HEAT WHERE YA THINK THE HEAT GOES? UP TO THE ATMOSPHERE AND SINCE CO2 IS HEAVIER THEN OXYGEN THE HEAT RISES THRU THE CO2 AND INTO THE AIR. CFC’S WERE A BIGGER PROBLEM
calm down luv #salty
Thanks for the article. Here from Mr. C
Mr. C <3 best teacher