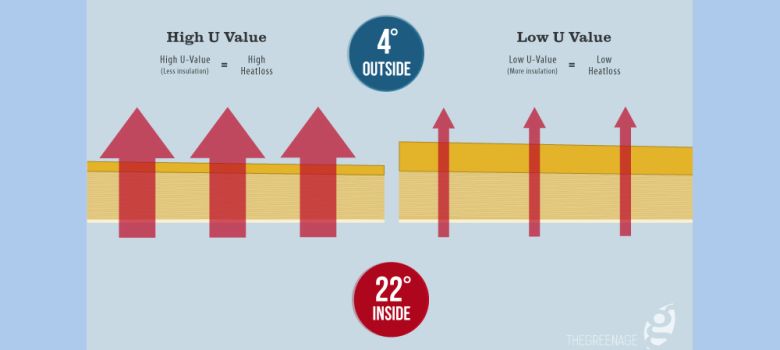
Getting to grips with U-values!
U-values might seem a pretty dull subject; however it is absolutely key that you understand them so that you can insulate your home with the most appropriate material. You can learn more about what a U-value is by clicking here.
The U-value signifies the heat lost through a given thickness of a particular material. You don’t really need to understand the mechanics of how it is calculated; instead it is useful to be able to compare different substances by their U-values.
The best insulating materials have a U-value of close to zero – the lower the better. Building regulations currently stipulate that for a new building, the elements must have maximum U-values as follows:
- Wall – 0.3 W/m2k
- Roof – 0.15 W/m2k
- Windows – 1.6 W/m2k
So in each section below we are going to examine each of the different elements and their typical U-values, we will then show you how to achieve the best possible U-values as stipulated in the building regulations (Part L).
U-values of SOLID WALLS
Solid walls were the norm in most properties built prior to the 1930s – unfortunately at this time energy efficiency wasn’t really on the radar, since fuel was very cheap. However, nowadays trying to keep this sort of home warm is very costly, so insulating them can considerably lower the heating bill.
- An uninsulated solid brick wall with a thickness of 225mm value will have a U-value of 2.70 W/m2k
- To insulate a solid wall you can either insulate internally or externally.
- 100mm of EPS insulation located internally or externally should bring the U-value of the wall down to 0.29 W/m2k in line with building regulations (in this example we have use EWI-PRO 100mm graphite EPS with thermal conductivity λ=0.032W/mk)
- To achieve this with rockwool insulation you will need to add about 110mm to either the inside or outside wall (in this example we have use rockwool 100mm with thermal conductivity λ=0.036W/mk) – obviously if this is done externally you will need to attach it firmly to the wall and it will need to be rendered. If you want to do this internally it is going to steal a large area of floor space.
- ThermaLine Plus is internal wall insulation (often referred to as dry-lining) attached to plasterboard and if you opt for the 40mm thick ThermaLine Plus you should achieve a U-value of about 0.65 W/m2k. This isn’t bad, but if you need to adhere to building regulations (i.e. it is a new extension for example) you are going to have to opt for something else.
U-values of CAVITY WALLS
Cavity walls became the norm in the 1930s. However until 1995, we assume that they were built but left unfilled (with insulation).
Unfilled cavity walls
- Unfilled cavity wall (built prior to 1900) will have a U-value of 2.0 W/m2k
- Unfilled cavity wall (built 1900 – 1975) will have a U-value of 1.6 W/m2k
- Unfilled cavity wall (built 1976 – 1982) will have a U-value of 1.0 W/m2k
- Unfilled cavity wall (built 1983 – 1995) will have a U-value of 0.6 W/m2k
Filled cavity walls – assumed post-1996
All cavity walls built after 1996 are assumed to have filled cavities as part of more regimented building regulations.
- Filled cavity wall (built 1996 – 2002) will have a U-value of 0.45 W/m2k
- Filled cavity wall (built 2003 – 2006) will have a U-value of 0.35 W/m2k
- Filled cavity wall (built 2006 – 2010) will have a U-value of 0.3 W/m2k
- Filled cavity wall (built 2010 +) will have a U-value of 0.2 W/m2k
Mechanisms for improving your cavity wall U-rating
- For a new build cavity wall to achieve a U-value of 0.2 W/m2k you would need to install 150mm of wool but this obviously means extremely thick walls – but this is the cheapest option available to builders.
- Using Celotex to fill the cavities is more expensive, but you will only need to use 100mm celotex to achieve a U-value of 0.2 W/m2k . The only thing to bear in mind here is that you still need to keep a residual cavity on the outside – but this means the cavity can be marginally thinner.
- The maximum U-value you can achieve by retrofitting cavity wall insulation in any property older that 1975 is 0.5 W/m2k since you are limited by the thickness of the cavity. In this instance to achieve a U-value of less than 0.2 W/m2k, you need to apply either internal or external wall insulation too, although you will only need to apply 50mm of celotex either internally or externally to achieve this.
- If you retrofit insulation in cavity walls built between 1970 and 1995, you should achieve a U-rating of 0.5 W/m2k.
- Any cavity wall after that date should already have cavity wall insulation as part of building regulations – the U-values of these types of walls can be seen above in the Filled Cavity Walls section.
Pages: 1 2
Pages: 1 2
This is a very useful article – thanks! Who can I link it to R-values? Any ideas?
how can you link it to R-values?
i think, one is the reciprocal of the other. so to get R values from a U value you divide 1 by your U value. as in 1/U value
Thats spot on niall
This is very useful, thanks for sharing!
Thanks for your comment scott!
What is the U value and R Value of a cavity wall such as this currently used in Middle East which containing 20cm of red brick +5 cm polystrene 35 density + 20cm of red brick ??
Which means that all cavity wall is 45 cm
Hey, thanks very helpful. Just found a case study of u-value measurements.
I am interested in the case stydy of U-value measurements. Please can you e mail me the site.
I am grtting frustered as i am not get anywhere.
Thanks
vimal
Hi Vimal,
What exactly are you trying to achieve? Maybe we can help?
Kind regards
James
“get close to that of walls or windows” mistake?
Thanks bob – yep that was an error on our part – now updated!
Hi James
Please could you confirm what the construction of the un-insulated cavity build is for the wall achieving 1.0 W/m2k and wall achieving f 0.6 W/m2k. I’m trying to work out what the u-value is for an existing wall with 100brick outer skin, 50mm clear cavity and a 100mm internal block work with 15mm plaster skim is?
Thanks
Tim
Very useful site for the u values of construction of recent years. Made calculations for compliance with current part L of the Building Regs much easier thanks Graham
What would be the u value equivalent to R 20 rating ?
0.05 – (1/R=U)
I live in a two level house built in 1910. It is of a random rubble construction and has a gap of between 3 and 8 inches between the inner face and the lath and plaster or gyproc dry lining (where that has been installed prior to our ownership). We also mainly have sash and case windows that I intend to retrofit with insulating units and draught beading. The house is listed which prevents changes that alter appearance.
I want a better wall performance without massive disruption to the family. Taking down plaster walls is absolutely the last resort and external cladding is a no no. I was thinking about PU foam or blowing in polystyrene beads. I’m worried about damp accumulation associated with PU foam so was favouring the beads. I’d value your thoughts and advice. Regards, Stewart
I am currently converting a garage into a kitchen extension, wet room and office and the external wall is 100mm. What is you advice with regards to insulation to bring this wall in line with building regs??
I am planning to dry line the wall using plasterboard with metal studs.
Thanks
Can you advise what effect that air circulation within the cavity wall will have on the U value, in both insulated (filled) and uninsulated (unfilled cavity) and especially when adding external insulation to a cavity wall structure?
It drives the u-value up something crazy!. The phenomenon is called “wind-washing”. Look up Mark Siddall on Twitter – he’s promoting an in depth article on this published by the Passivhaus Trust. It has good pictures in it. Essentially if you are adding EWI, you have to fill the cavity first to effectively make it a solid wall. Use polystyrene beads because if any moisture gets in there it can drain down and out. DOn’t use any other type of cavity insulation as you can lock in problems with those.
Thank you for a good article regarding U values. Currently building an kitchen extension, I am confident that 100mm Kingspan or Celotex insulation in cavity walls will provide a superior performance to glass/rock/earthwool of equal thickness. Now wool insulation has excellent acoustic properties, I do not find information regarding acoustic properties for Kingspan and or Celotex cavity wall insulation, which makes me wonder if a combination of wool and Kingspan insulation would provide the best thermal and acoustic properties? Say wool in the cavity and kingspan on the inside or outside wall?
Congratulations – delighted to see it. I spent nearly all my career in the construction industry – where I conceived a considerable respect for the Building Regulations and the people behind them. Then I retired to France, which enhanced my respect – oh, how they are needed here……
In my experience the builders and house-builders themselves failed to appreciate who their best friends were – there must have been times when the BR people were all too aware of this. In the meanwhile, though, you’re doing a splendid and desperately, increasingly, needed job (even though I don’t offer favourable odds on external insulation…..). The content of your website’s excellent, if I may say so; equally if I may say so, it would perhaps be good to balance the influence of the double-glazing salespeople with some objective figures on window insulation (which is to say its near-impossibility…..). Erm.. you do talk, under Mechanisms for improving your cavity wall u-rating, of achieving a maximum U-value – woops?
I think your technical advice is first-class
All best wishes –
Peter Firth
Hi There hoping someone can help me out?
Is 100mm thickness of an insulation material, thermal conductivity 0.04W/(m.K) equivalent to 50mm thickness of an insulation material with thermal conductivity 0.02W/(m.K)?
Thanks
Matt
Can you help please. I have a court case soon whereby the builder on my extension, did not put enough insulation in roof or floor, despite it being done under building regs! Are you able to tell me in the difference in u value losses into a financial figure i.e. If door was shut from extension into remainder of house and heated to 21degress c, over a period of six months, what would the increased cost of heating be in that room.
The figures are 0.37 u-value in my pitched roof instead of 0.17; 0.32 u-value in my floor instead of 0.19.
Nobody seems to be able to work it out. Thank you ASAP please. Shirley Gale
Basically you have to work out what it would be for say an hour for each equation. Take one away from the other and multiply roughly by the number of hours you would be heating the room during the six months.
Sorry read your email wrong was just scanning but still an building inspector should know this.
It sounds like you need to get a building inspector into write a report for you. It is the same type of person who does a report for you when you are buying a house its just more detailed and room specific. But any estate agent, google or yell should help you find someone in your area. Can’t understand why your solicitor hasn’t organised this. You then need to check the paperwork and planning outlines from the builder who did the work. Your plans should state what thicknesses the builder planned to do your roofs and wall etc and the inspector should confirm whether or not it was done to this standard. Your solicitor should have sorted this out for you.
I am in the process of having my conservatory roof replaced using a WARM-ROOF conversion. Some vendors are promoting a 5% VAT rate but many are not. My preferred local fitters do not offer this but had they done so it would save me about £750. How do I go about recovering the difference, is it from the local authority or should I tackle the vendor/contractor. (Having only just discovered this fact and have already paid a large deposit.
Hi there, you need to go back to the contractor and find out why they are not offering the reduced VAT rate.
Is that 1983 date correct? The article you published later (February 6 2015) said the regulations changed in 1985, not 1983. Which one is correct? And do you know which month in the year the change came into effect? (I ask because I’m in a block that has a plaque saying June 1983 and I want to check which regulations were applicable when it was built.)
I am being offered free CWI usIng thermabead basic, my house is 1995!build but with no cavity infill even partially. I am apprehensive as i residenin a zone 3 location according to a windswept zonal chart and preTty much exposed on westerly southerly sides
I am told that thermbead does not alloW passage of penetrant rain but i am highly sceptical whats the view On Here?
I am thinking of treating My walls with breathable brick water repellant , would this alleviate the tHreat?
this was so clear and easy to understand thank.
would have been nice to have floors included too.
Mark
Your definition of U value seems to be confused with R value. U value is the heat loss per degree temperature difference for a given completed building element per square m (eg a brick cavity wall with 80mm of kinspan. Hence the thickness is not relevant. R value is thermal resistance per m of thickness for a given material. Eg a wall of given construction has a U value the brick the wall is made of has an R value.
Hi can you advise me the best way to insulate a internal wall the existing is 9″ solid and meets a extended cavity wall .Is a foiled foam insulation better than using batterns and multi layered foil insulation. I have no damp problems. Another possibility that has been suggested to me is place membrane against the wall then 25mm celotex fix by 25mm treated batterns over the top and inserting 25 mm celotex I between these battens then the plasterboard . Please would you advise
Hi, I am building a house and am planning to use 100mm stone external wall, 100mm concrete block inner wall, and between them a 150mm cavity into which I plan to install 100mm Celotex boards. 2 questions please:
1- Will this give me the desired 0.2 W/m2 K?
2- Because of the un-uniform courses of stonework on the outside that I am planning to use, I’m keen to find a wall tie that will screw into the inner concrete block, hold the 100mm insulation board in place, and tie in the outside wall. I am looking at Bluebird Cavity Wall ties to do this. Can you recommend them, or indeed another product to achieve this?
Many thanks,
I have a building, a church, which I want to convert to a pair of semi detached houses, the walls are brick inside and outside with a 100mm cavity, what insulation would I
I need to meet building regulations.
Hi. I don’t see mentioned anywhere here the risks of condensation developing when insulation is fitted in upgrading work. This is an absolutely vital area to fully consider.
I heard that u-values need a full accreditation to be official, is this true?
It is true, Connor. If you need an official U-value, you can give us a call. We have the necessary qualifications to give official U-value calculations 🙂
What is the U value and R Value of a cavity wall such as this currently used in Middle East which containing 20cm of red brick +5 cm polystrene 35 density + 20cm of red brick ??
Which means that all cavity wall is 45 cm
Really useful article, thanks
Do you use the thickness of only the insulation board for example 60mm or do you use the thickness of the full system so 60+12 = 72mm rather than 60?
Very useful site. Many thanks.
My house was built in 1951 with cavity walls. The cavities were filled with some kind of insulation round about 1980. What is the U value liklely to be? Lots of unknowns I realise so just trying to get a rough idea.
if i have more than one type of insulation in a wall does the lowest uvalue go to the inside. e.g. from inside 40mm eps then 100mm rockwool
75mm Gypsum partition U Value ??
50mm Aluminium channel with both side 12mm thk Gypsum board and between area have glasshool.
I think people need a greater understanding of how old properties work. In relation to the use of lime mortar, render and plastering. I was told specifically by a technical expert at Super Quilt “solid wall buildings do not need to ” breathe” . ” This lack of understanding between the difference tin modern cement built properties and lime built properties is fundamental to the understanding of how best to insult older buildings… The building industry has been doing destroying old properties for decades. Old houses get cement rendered, re pointed in cement that is harder than the bricks themselves, The walls can’t shed the water and degrade resulting in damp cold walls and blown brick work. People also get advised to adopt the wrong insulation products using PIR boards, foils making the spaces air tight and trapping the vapour resulting in mould spores within the walls an d living environments simply in an attempt to meet the required U values… Also a U value cannot be simply given as a blanket if you do this you get this it must be site specific determined by a vast amount of variants. It all seems somewhat pointless unless actual physical measurements are taken of each property prior and post completion of said works.
The U value attributed to solid walls of 225mm or greater was guestimated. There is no science behind it. The damage being done to older properties by insulating is ridiculous. Walls after the 1830’s – 1950’s were built using high density hand made bricks (in the main as those that were not have long fallen into unretrievable decline). These bricks have recently been tested to show a U value approximately quarter of that quoted here (about the same as a 7.3N concrete block). Whilst the lack of air gap and insulation is a problem, you should not immediately install insulation it is better as stated above to let the wall breath. This also helps with damp.
In a house designed for radiated heat (IR) it may also be better to not have plaster as this does not take the accumulated heat and hold it where a solid block (brick) does (we have an eco house on the property but that is another story for another day). This we heat with half a Kw during the winter months.
A south facing solid wall will radiate heat into the property continuously year long. Whereas an insulated wall will not. In the 1990’s and 2000’s a lot of work was done at the houses of the future project at Loughborough and Nottingham Universities but is now largely ignored.
My House (as part of a project) was installed with embedded sensors in every room and those on the South Face/SW and SE to a lesser extent (where solar glass was installed) kept a temperature between 11 and 13c in the winter (13 year survey/average). Temperatures in November and December remain high (we put this down to retained heat in the wall) and gradually decline in Jan/Feb…. by March the walls are heating again.
The roof has recently been (super) reinsulated using Kingspan and multi layer foil and high density foam backed boards to give a U rating of 0.09 and last year the average retained temperature was 16c (the heating is set to come on at 8c (Schneider Wiser) and it rarely did so throughout the winter (mainly late February).
We are on tank gas at 32p a litre and we use about 1800 litres a year and we have a log burner in the Living Area (North side of House).
Chris
Totally in agreement. No mention of cork anywhere to be found as a natural option. All the polystyrene being legally stuffed into walls rebukes ‘breathability of lime wall aka breathable walls. Some people wear pure wool jumpers others acrylic for all enviro-mental purposes sheep have been around for yonks i.e. nature provides the answer. Why this emphasis on cheap cheap cladding is a waste of natural resources & not really taking future generations into account qua environ-mental.. AFFORDABLE housing means signing an agreement wearing pure wool, silk, cashmere,alpaca, in the winter, turning the heating down. There is a feel good factor in living in spacious house which no rabbit hutch could replace. Adding lime to cement mix ensures breathability. How are earth walls calculated qua R & U factors which please buildings regs ?
Hi, good article!
It would be usefull on this site to have a simple but comprehensive sorce of information to allow calculation of “U” values for any combination of building materials:
A simple table of materials with “K” value followed by “R” value for thicknesses likely to be encountered.i.e. brick 100; clay brick 100; dens block 150, 125 100, 75; hollow blocks, diff density block; render 20; plaster (bonding+finnish)20; plaster board on dabs 15; PIR 20, 25, 40, 50, 75, 100; blown cavity fills 40, 50, slab fills; part fill insulating materials thicknesses; air gaps diff widths, sealed / vented; inside / outside / intermediate surface resistances for yhr different materials. A simple explanation of K R and U and worked example to show how a simple or more complex wall can be easily calcilated.
“Unfilled cavity wall (built 1900 – 1975) will have a U-value of 1.6 W/m2k” what r values are you using to get that u value
How do we find our u-value of a property built in 1960’s after cavity wall insulation was put in in 2014? The company who installed the cavity wall insulation no longer exists, and NICEIC who provided a Certificate said they can’t help. We want to fir exterior cladding but the building inspector said he needs to know the u-value before we can start, as we may have to add exterior Celotex before installing the Eurocell Composite Coastline Cladding. Is there a company near Chichester who will visit site to assess our cavity wall U-value.
In the paragraph above where it states ” retrofitting CWI in a property older than 1975 you can only acheive 0.5″ this statement is not quite true.
In fact ,if you used injected closed cell PU Foam you could easily get 0.3 in a 70mm cavity. in 35 years of injecting foam i have found very few properties with cavities smaller than 50mm and even these when filled with closed cell foam will give at least 0.43.
We are looking at using closed cell polyurethane to fill our 1950 brick built house cavities, which are apparently 90mm thick. So what u value do you think we could achieve with that? Because we are in a very exposed coastal spot, I was considering cladding the front of the house with Marley eternit cladding, with a layer of super foil insulation below it, to give a bit more oomph. Do you think we need the extra YBS super foil layer on top of 90mm closed cell polyurethane, or would that be enough? Yes it will all cost a lot of money and I am looking at doing it in stages. A bit worried about the loss of solar gain, but we are on oil central heating, so ….
What is the ‘u’ value of a solid wall set in a cutting of a hill-hence nestled in an incalculable amount of earth? 1930’s single storey build – interior : 3 bone dry walls- what would be a viable option qua insulation ? Please nothing with polysterene balls! Is cork plus plaster boards a viable option?
Hello
Can anyone tell me what the u value is for a 9″ (225mm)cavity block wall the blocks with the 2 cavities in each block?
I hope you can help me,
Thanks for now Frank Maguire Plumbing & Heating Lecturer, Dundalk Institute of Technology Ireland,
I am restoring a victorian house with no cavity walls. Internally I have installed 70 mm batons with a 60mm gap between the batons and the external walls. The batons are ready to accept the insulation boards. However I now need to install electric cables for sockets and lights as a first fix. Do I connect the cables in the air gap to the exterior wall and bring them through the insulation boards. OR do I install the cables to the front of the insulation board i.e. sited just behind the plaster board when that is installed. I am reading that if I puncture the insulation boards and bring the cables through towrds the room it will negatively affect the U value.
Does anyone know the U value of clay lump, as used in older houes in Norfolk. It is a clay/straw mixture.
Excellent article. Clear, concise and comrprehensive – thanks so much.
Correct me if I’m wrong, but the maximum u-values here are not particularly relevant. When building to regs you need to achieve the notional dwelling u values, the maximums are there only for when an individual element needs to be higher. The rest of the building would then need to be improved such that the overall building achieves the notional example heat loss. The notional numbers are much lower, 0.18 for walls, for example. People should aim for the notional dwelling numbers (table 1.1 in part L), not the maximums.
Are there different U-values for different types of cavity wall insulation? My new home was built in 1935 and had white, light, woolly fibres injected into the cavity in 2008. It’s my first winter here and the place is freezing.
Hi
Although a novice in these matters, i wish to dispute this article.
You say a solid 225 brick wall has a U = 2.7, however I should point out that a single brick has an R value of 1.35 therefore double brick R = 2.7
U = 1/R, 1/2.7 therefore U =. 0.37. Big difference.
Regards
Dave
I have a 1960s cavity wall. Brick on the outside. Concrete block on the inside. I am guessing from this article that the uvalue is therefore around 1.6 as per this article. The wall is then rendered inside and out with a sort of concrete based render and the render is about 1cm thick inside with a plaster skim on top (no idea outside, I think its thicker). I have been told adding insulation board INSIDE my external walls will bring the u-value to a similar level as filling the cavity. Since all the walls need replastering it does two jobs at once. Using the u values and thickness of different types of insulation board, how can I check this calculation and what the thickness would need to be to achieve building control levels? Thanks!