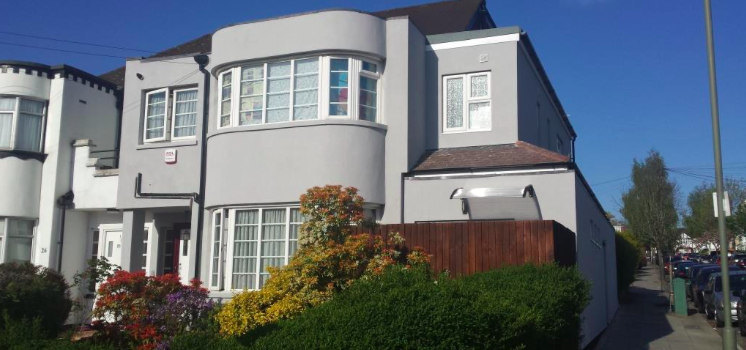
Is this the best way of doing things on new builds?
The answer not necessarily – certainly not since the availability of external wall insulation systems. External wall insulation is now often applied to new builds to to ensure the buildings comply with all the thermal insulation requirements for building regulations.
What about retrofit projects?
Even if one is planning a retrofit project, gone are the days that insulated plaster board would be the ‘go-to’ solution for solid brick properties; OR cavity wall insulation for post war construction. External wall insulation systems have been approved for use not only with new build constructions, but pretty much any building fabric type.
These new options make the scoping exercise for architects a much more fun prospect.
External wall insulation systems have the perfect insulating materials
External wall insulation systems are comprised of a range of external wall renders and insulation products. At their heart are the insulation materials themselves. This focus should appeal to most architects.
Most external wall insulation systems have the lightweight expanded polystyrene system (EPS) as the main insulator. It not only slows heat transfer but is also one of the most cost-effective systems available on the market today. If not using EPS, the Mineral Wool system also has unparalleled acoustic insulation properties and can be used on non-standard construction types such as timber frame. The open vapour insulating materials are all breathable, and therefore perfect for insulating even the oldest properties in the UK housing stock.
External wall insulation dual benefit – robust finish
Most external wall insulation systems allow for a flexible basecoat or adhesive layer with embedded fibreglass mesh. This differs from traditional renders, which are based on sand and cement and miss out this new innovative process. The basecoat layer allows the finish to remain robust and work with the natural movement of the building so that cracks do not appear anytime soon.
Some external wall insulation systems also produce heavy duty renders that go on top, allowing for even the most highly exposed areas to be insulated.
If the applicator is using mineral or silicone-based renders, these are breathable, and should be less prone to discolouration or cracking in the long-run.
External wall insulation allows for 100s of different finishes
Whether you are speaking to a customer about constructing a new build or planning a retrofit project, the customer will always want options on how the building looks like when the project has been completed.
External wall insulation system suppliers can supply dozens of different finishes, with 100s of different colours as well as different types of renders – acrylic, mineral or silicone being some of the most common ones.
Mosaic renders can be used on specialist areas of the property such as the plinth, parapet or on concrete sills to give a premium finish.
The benefits don’t stop there!
Customers may be worried about losing out on the ‘brick effect’ on the front of the property when rendering. Thus, external wall insulation manufacturers have started to produce specialist brick-slips, which can actually go over the top of the insulation and help the building retain its original look.
External wall insulation can save on time and money
Imagine a new extension or side-return being built: with standard cavity wall insulation the outer wall still has to be built out. With external wall insulation systems, the insulation can go straight on top of the single skin of block or brickwork.
The external wall insulation systems are installed with adhesive on the back of the board and enforced with mechanical anchors that go through the insulation and are ‘keyed’ into the substrate. This is the most common system of installation of external wall insulation on standard buildings. There are other methods such as ‘dry-fix’ or railed systems which can be used in certain scenarios. The best bet is to consult the materials manufacturer when at the planning stage.
Choosing a rendered finish instead of building up the outer wall with decorative brick can actually save you time and money. To do a relatively simple external wall, with a skilled applicator should take a few days. The only added time is to build in waiting times for the various layers as and when they are being installed.
External wall insulation reduces the risk of interstitial condensation
Interstitial condensation can occur in the fabric of the building inside walls, roof or floor space. Interstitial condensation occurs when warm air meets cold air inside the fabric, forming a dew point, where the liquid condenses and forms condensation. This is different to surface condensation or thermal bridging where condensation appears on the outer or inner surface of the wall area (this is where the dew point would be).
External wall insulation will form a barrier on the outer leaf of the wall and reduce the risk of a dew point being formed within the wall. Internal wall insulation doesn’t have this benefit, and some would argue that it actually amplifies the effect of interstitial condensation with the wall fabric.
Are there RIBA approved external wall insulation systems?
The short answer is no – RIBA is the professional association that sets standards, provides training and supports architects to the advancement of quality in buildings.
The BBA or the British Board of Agrement, on the other hand, is the body that tests and certifies building products to ensure they can be used in new or existing construction projects. For example, external wall insulation systems such as EWI Pro Insulation, Baumit, Sto and Weber are some of the best-known products on the market.
We would strongly encourage architects, developers or funding bodies for construction projects to work with the external wall insulation system designers to help with the planning exercise before any projects kick-off.
Marta Banovich, EWI Pro Insulation Operations Manager, said ‘Our doors are always open to architects or other project managers who want to learn more about our external wall insulation systems. The demand for specialist training has increased in 2016 more than any other year, and it is due to this increased interest that we are providing product familiarisation courses at no charge to anyone who wants to get more information’. EWI Pro Insulation Systems were kind enough to share some of their typical system drawings, an example of the finish of the base of the property can be seen below:
How can the GreenAge help with external wall insulation?
TheGreenAge has experience working with contractors to oversee specific external wall insulation projects and funding schemes, as well as working closely with manufacturers of external wall insulation systems to help them with various certifications, compliance and industry harmonisation projects.
As we have been and still are at the heart of the external wall industry, we are the perfect platform to give information about the benefits these systems can bring.
If you are interested in learning more about external wall insulation systems and their benefits, simply fill out a form and we’ll email you an information pack.
No Comments yet! Be the first one.